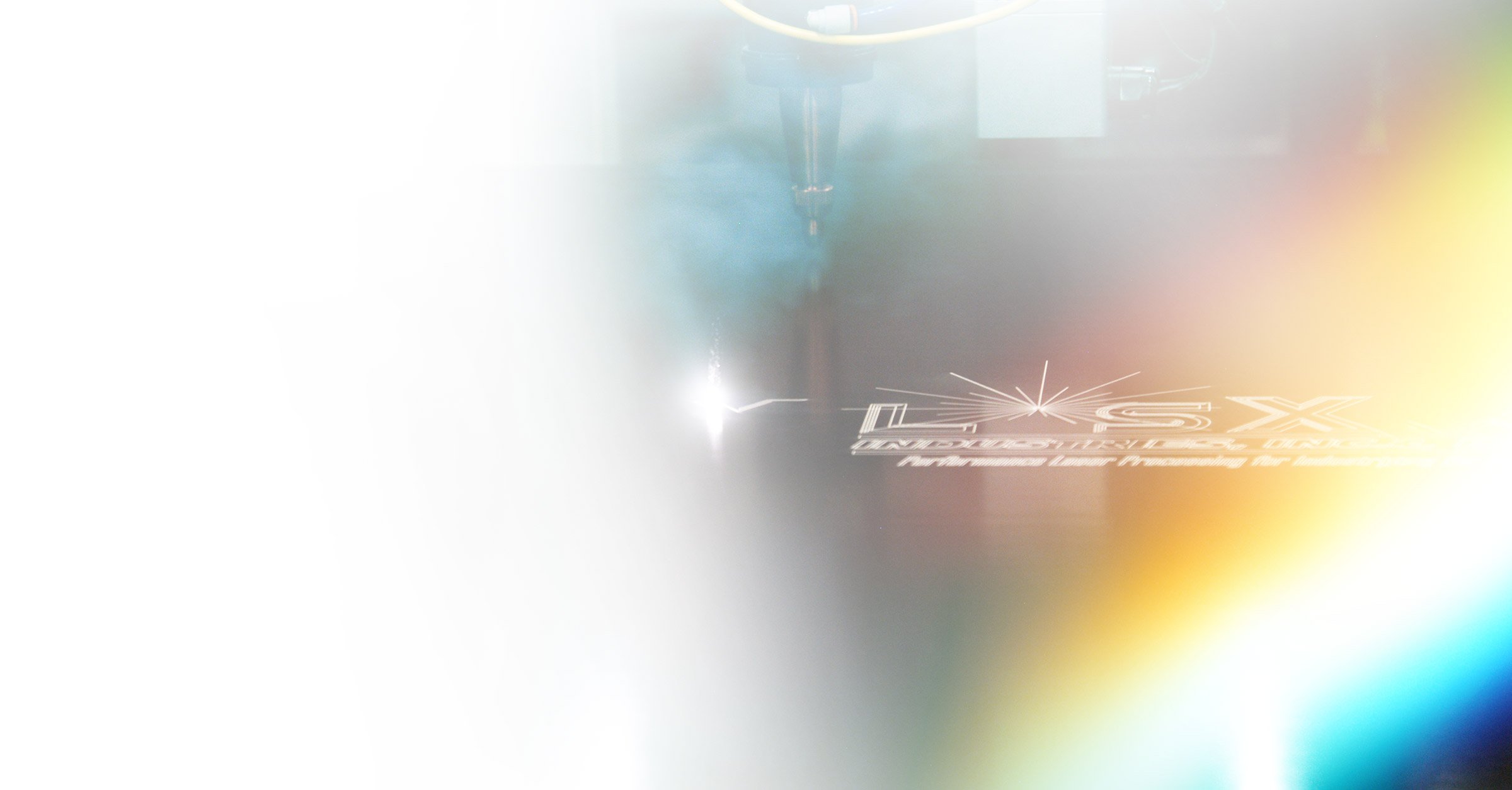
Why laser technology?
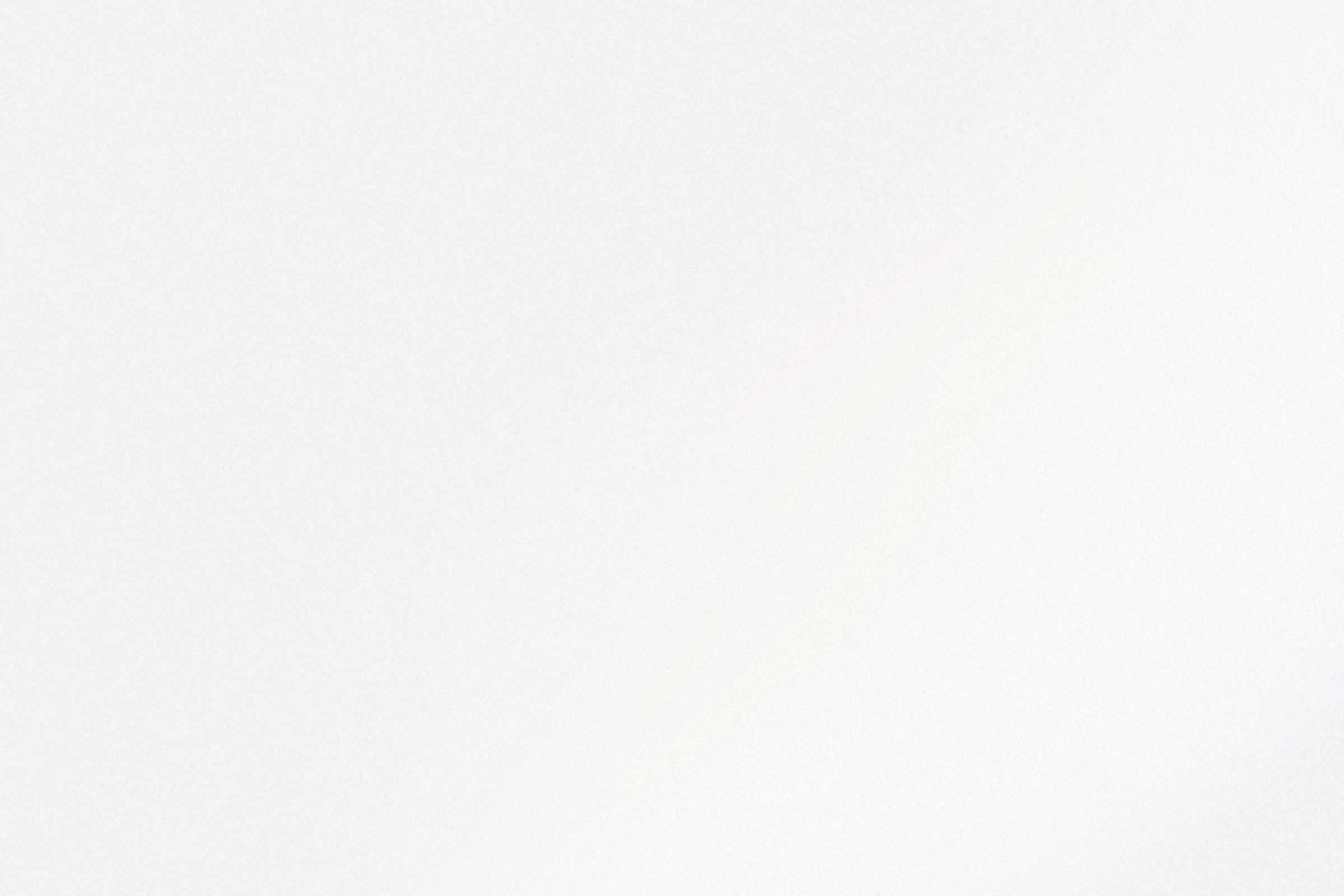
Elevate material processing in a digital age.
Material flexibility
Lasers offer immense flexibility for traditionally difficult to process materials such as extensible, pressure-sensitive, and abrasive materials.
Design flexibility
By replacing the time- and labor-intensive tooling process with digitally reconfigurable lasers, you can inexpensively prototype and iterate.
Precision & intricacy
Lasers offer a tool-free, non-contact method for rapidly performing precision cutting of intricate parts not possible with hard tooling.
Future-proof investment
Digital workflow capabilities enable multiple processes in a single station and do not require retooling equipment as customer requirements evolve and new materials emerge.
System longevity
With lasers, you do not need to plan for costs associated with tool wear and maintenance, making production costs, downtime, and equipment lifetime easier to calculate.
Waste reduction
Laser processing maximizes material utilization by nesting parts on common cutting lines, which when combined with vision registration, greatly reduces material waste.
Prepare for the future with laser.
-
As smart manufacturing techniques and automation become essential for manufacturers, laser material processing also must be included in intelligent workflows. At LasX, we recognize this and know that our LaserSharp® Processing Modules enable truly digital workflows. This technology eliminates tooling that requires specialized knowledge to develop and maintain, removes lengthy changeover times, synchronizes to digital workflows, and enables just-in-time coordination for converting. As a result, we are facilitating a fully digitized converting and finishing process that allows manufacturers to implement intelligent, integrated workflows from beginning to end.
-
From enabling more efficient techniques that reduce material waste to our forward-thinking vision of ensuring laser processing of environmentally friendly materials, the LasX technology roadmap is committed to promoting sustainability initiatives. Our lasers are digitally reconfigurable, so as material and processing requirements change, waste is reduced as dies do not need to be changed out and discarded. Lasers also provide non-contact cutting and auto nesting capabilities that improve material utilization by up to 20 percent. For recyclable and compostable packaging applications, our laser processing of mono-materials dramatically reduces the amount of waste going to landfills. For etching applications, our laser etching offers a more environmentally friendly approach by removing the need for chemicals to etch metal foils or electronic circuits.
Our Laser Processing Capabilities include:
Through-Cutting
•
Drilling/Micro-Perforating
•
Scoring
•
Ablating
•
Kiss-Cutting
•
Etching/Marking
•
Through-Cutting • Drilling/Micro-Perforating • Scoring • Ablating • Kiss-Cutting • Etching/Marking •
An Ideal Tool for Many Applications and Industries
Laser material processing delivers tremendous benefits over mechanical approaches.
Lasers complement a variety of materials
-
Papers
-
Plastics
-
Adhesives
-
Metal Foils
-
Textiles
-
Foams
-
Nonwoven Fabrics
-
Silicones
-
Urethanes
-
Ceramics
-
Polyester Plastics
-
Polypropylene Plastics
-
Polycarbonate Plastics
-
VHB Adhesives
-
Silicone Rubber
-
EDPM Rubber
-
Butyl Rubber
-
Neoprene Rubber
-
Nitrile Rubber
-
Teflon
-
Mylar
-
Nylon
-
Kapton®
-
Kevlar®
-
Felt
-
Leather
-
Cork
-
Graphite
-
Elastomers
The Evolution of Laser Technology
FAQs
-
The typical cutting speed for LasX equipment is 4,000 mm per second (100” per second). Speeds will vary based on the material type and material thickness being processed. We also can “gang” multiple lasers to increase cutting speeds and/or material widths while operating under a single LaserSharp® control interface.
-
Our LaserSharp equipment solutions typically range from $100,000 to more than $1 million USD. If you would like to immediately test our equipment for your specific laser application, we are also happy to quote you on our contract manufacturing or confidential process development services.
-
We recommend chatting with our laser experts about your specific application requirements. We can then guide you to our contract manufacturing services to develop your laser material processing application and test run your requirements – an approach that will dramatically accelerate your development and maximize your ROI when investing in a LasX equipment solution.
-
Fundamentally, our laser technology enables the production of as little as one part and the ability to queue up and process any number of unique parts without stopping.
-
Since we design our LaserSharp equipment with complete vertical integration of process controls, LasX can always upgrade the laser technology to be consistent with current state-of-the-art processing techniques. This means your equipment can easily run for more than 10 years. Our ClearCut® service plan can help you further maximize equipment uptime, performance, and lifespan and ensure you will realize maximum productivity through services such as machine health-checkups and on-site laser process development and operator training.
-
LasX LaserSharp Processing Modules (LPMs) are the engines that power our high-performance laser material processing equipment. Our powerful LightGuide operator software directly imports several design file formats to guide the laser beam around the material with no special file preparation or handling required. LasX standard LPMs can be configure with CO2 lasers, fiber lasers, UV lasers, and femtosecond lasers and can continuously process materials from 100 mm (4”) wide to more than 2,000mm (80”) wide.