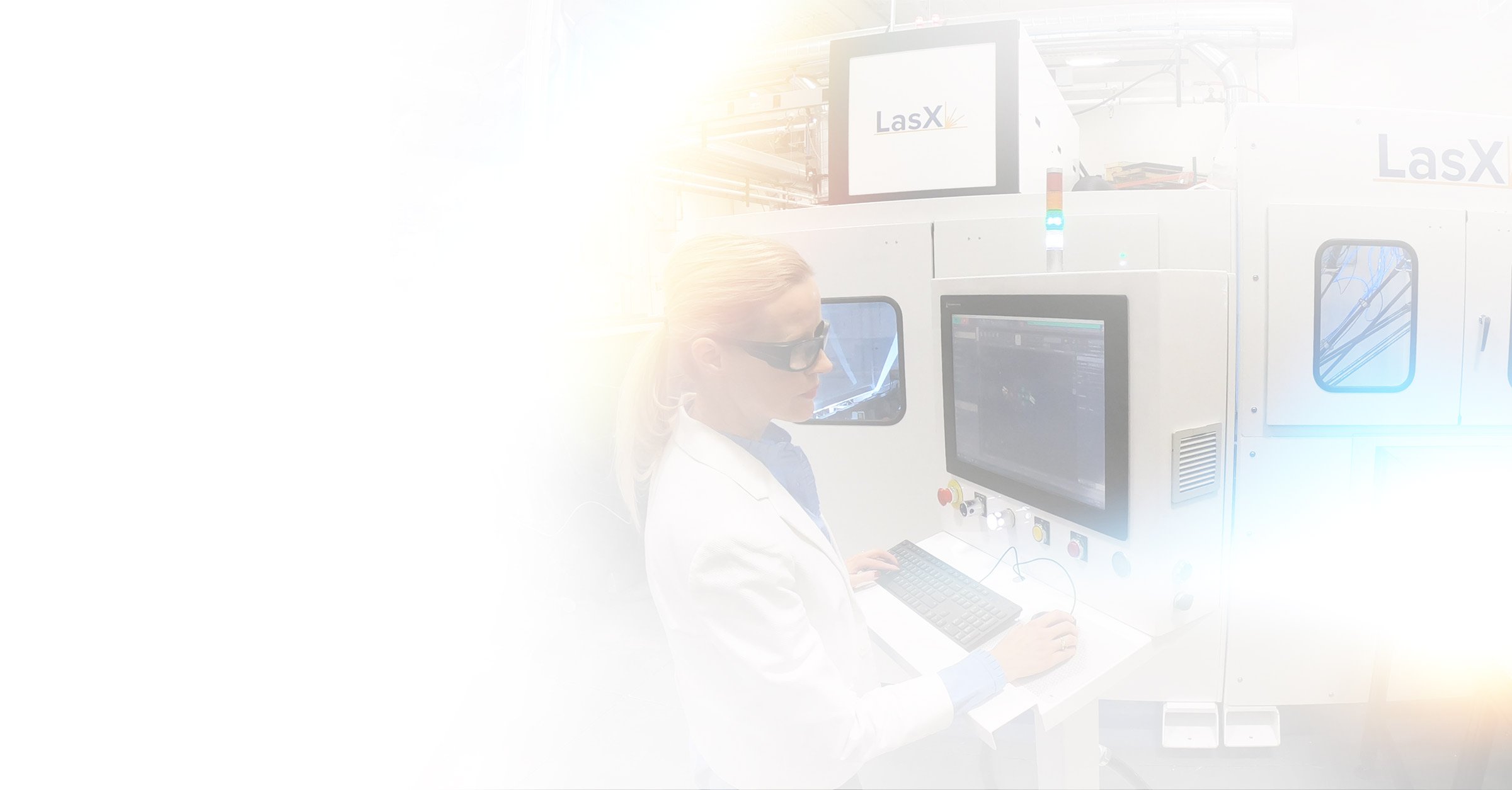
Why LasX?
Access our industry-leading technology stack.
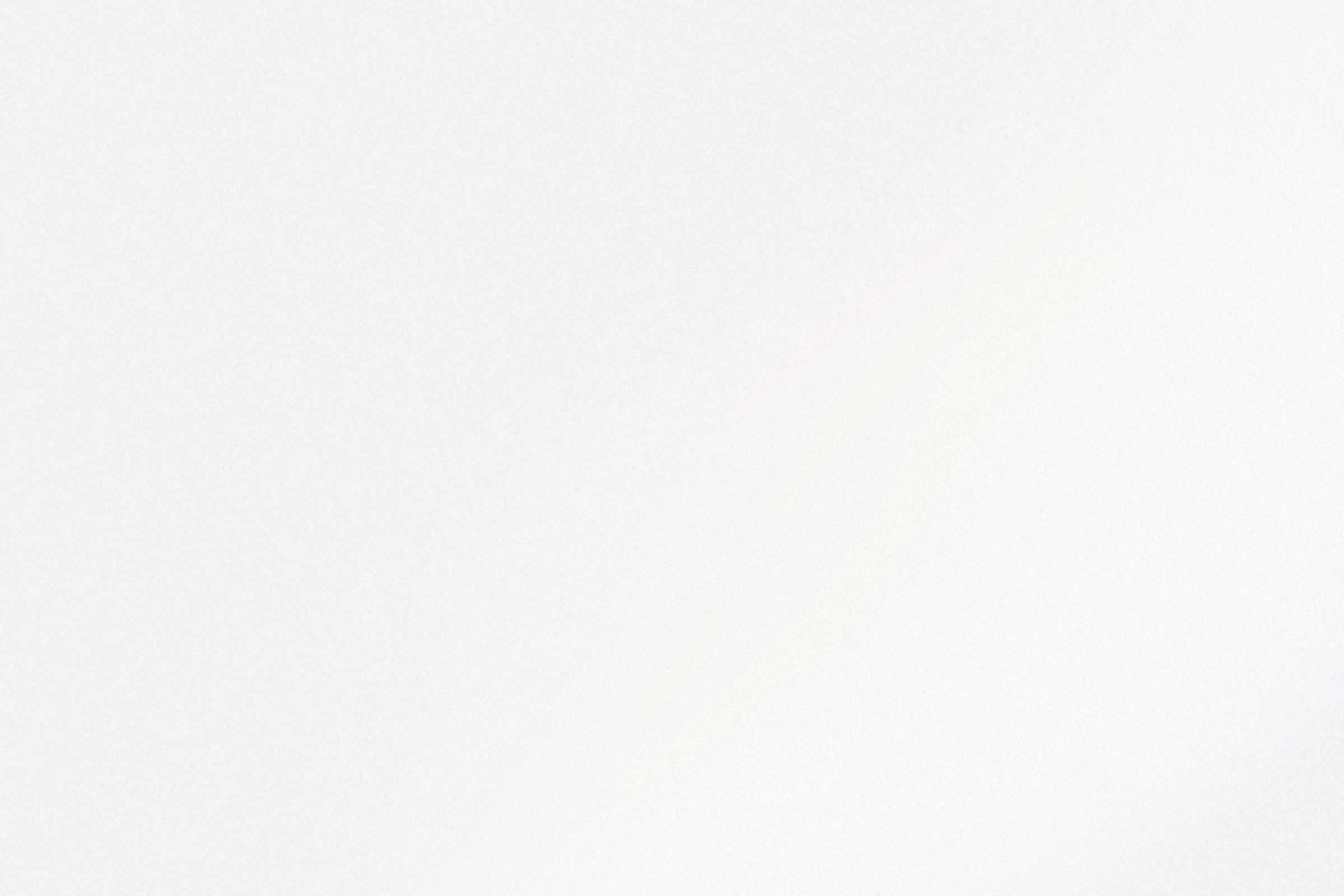
LasX delivers a powerful technology platform.
Our technology platform is sophisticated and nimble. Powered by LasX's core engine for material processing — the LaserSharp® Processing Module (LPM) and our intuitive LightGuide® operator software, LasX equipment can be quickly configured, and reconfigured, to meet your exact and ever-changing application requirements.
What can our core technology do?
Quick Facts
meters/second processing speed
4
meter wide material processing
2
years equipment longevity
10
sophisticated LPM options
3
Industrial Process Controller
-
Proton plays a key role in delivering capabilities not seen in other technology solutions including: high-speed on-the-fly laser processing, vision registration, true order-of-one processing, and model-based laser depth control.
LaserSharp Processing Module
-
LaserSharp Processing Module (LPM) combines a laser source, power supply, focusing optics, beam scanner, patented Proton process controller, and LightGuide software into a single package, making it easy to integrate laser technology into your manufacturing workflow.
LightGuide Software Interface
-
LightGuide is the link between the user and the machine. Its interface allows users/operators to upload designs and projects in a variety of formats — pdf, .dxf, .dwg, .svg, .jpg, gif, tiff, bmp — for production.
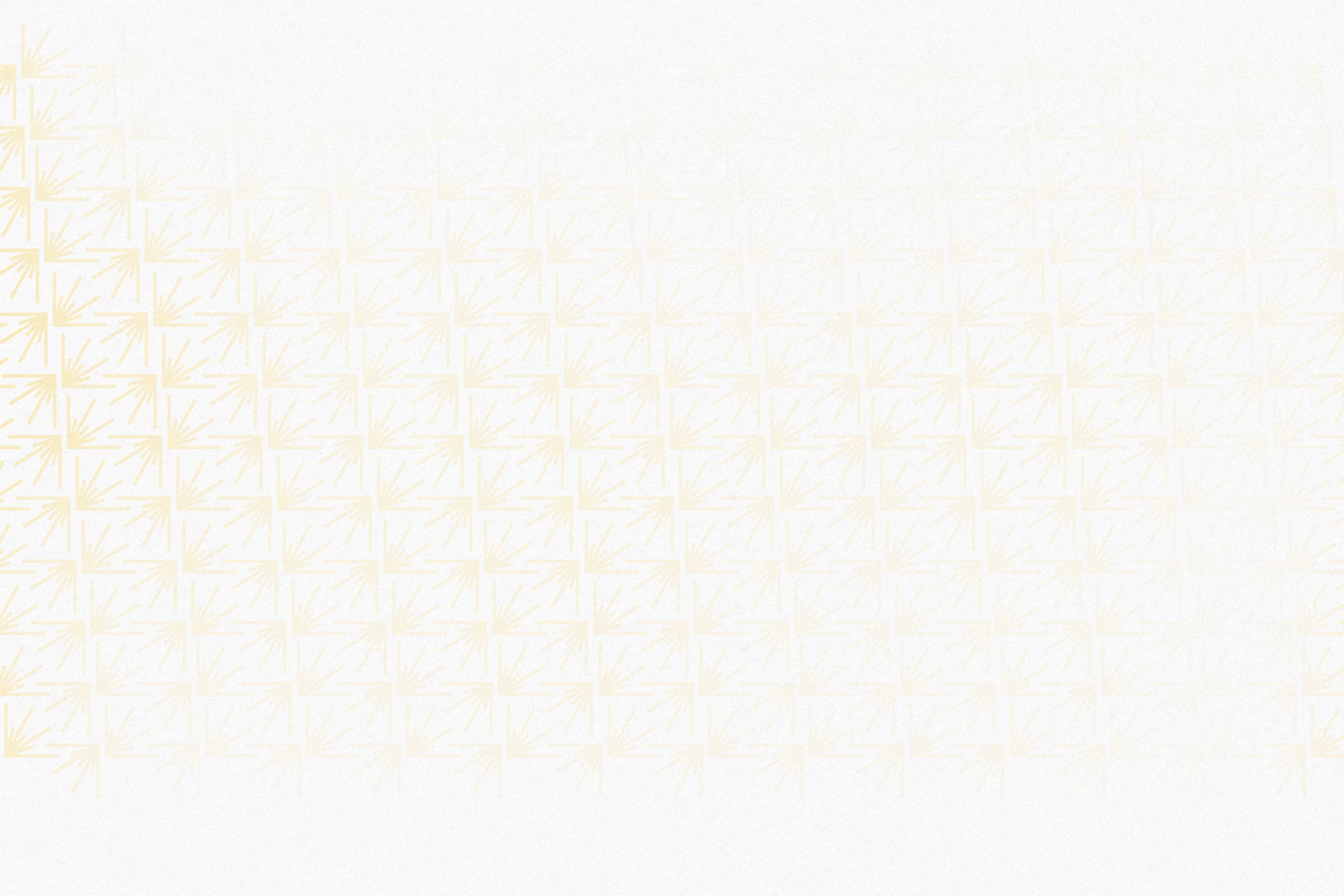
The LasX Difference.
-
Ranging from flexible electronics to medical packaging to high-speed marking and etching, LasX casts a wide net of expertise.
-
With our automated digital workflows and lifetime equipment upgrade program, you have the flexibility to perform multiple processes with a single solution without retooling equipment as your production requirements evolve and new materials emerge.
-
By using LasX lasers to perform on-demand, high-speed non-contact material processing, the costs associated with die cutting’s tool wear and maintenance are now a thing of the past —lowering your production costs and set-up time and extending equipment lifetime.
-
Our laser technology maximizes material utilization by nesting parts on common cutting lines, eliminates the chemicals typically required for etching on metal foils and circuits, and can be configured to process emerging materials.
-
LasX is not your typical equipment provider. Our contract manufacturing facility uses the same proprietary technology that powers the equipment solutions we build for customers around the world. We are always iterating on our technology to maximize performance.

Robotic material handling
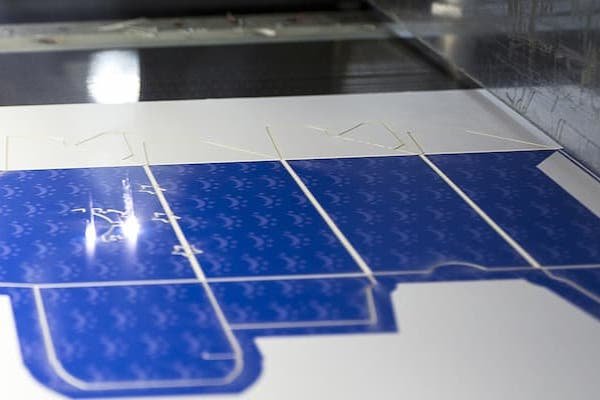
Folding carton finishing
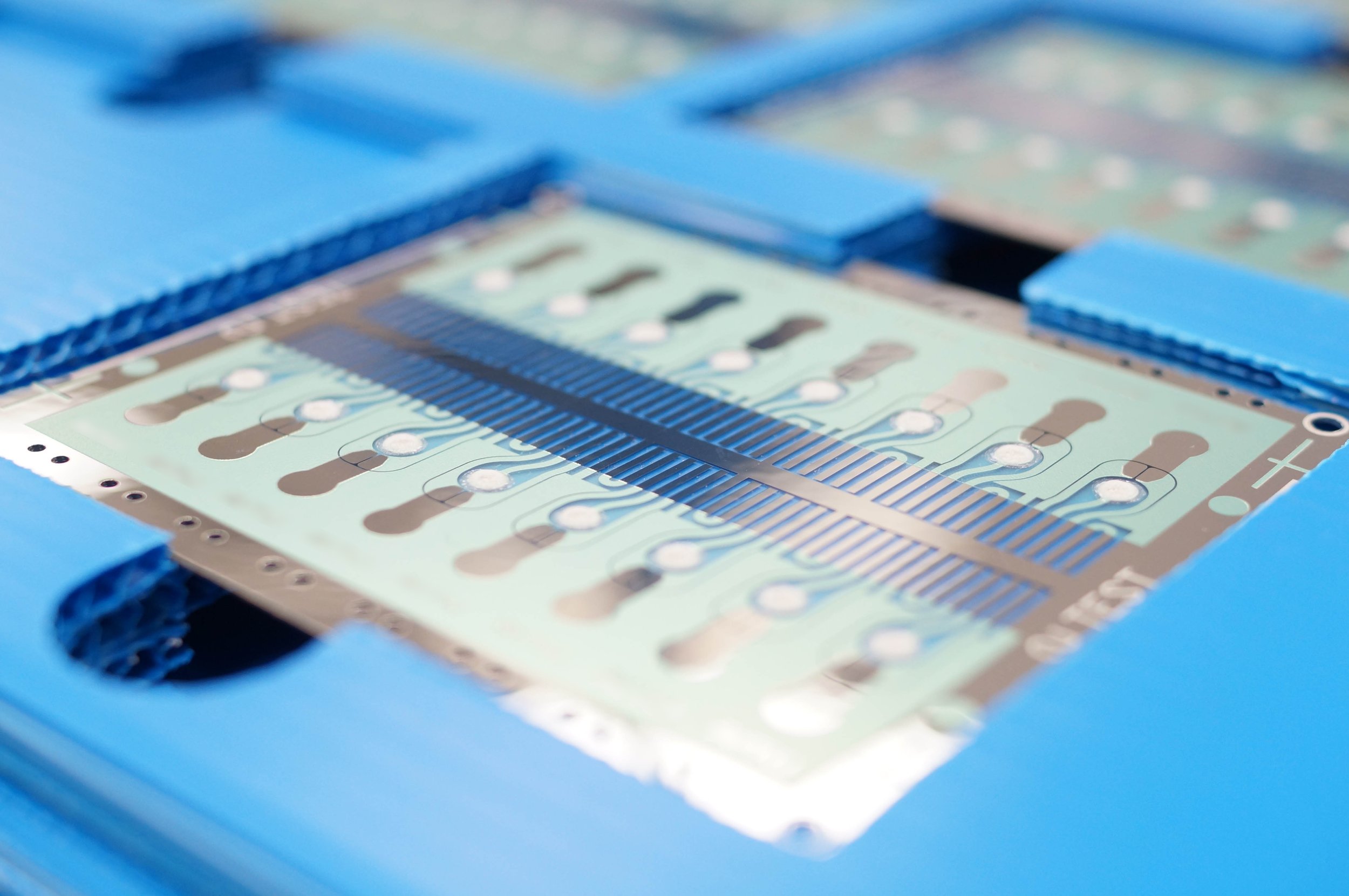
Precision cutting of medical components

Foil processing
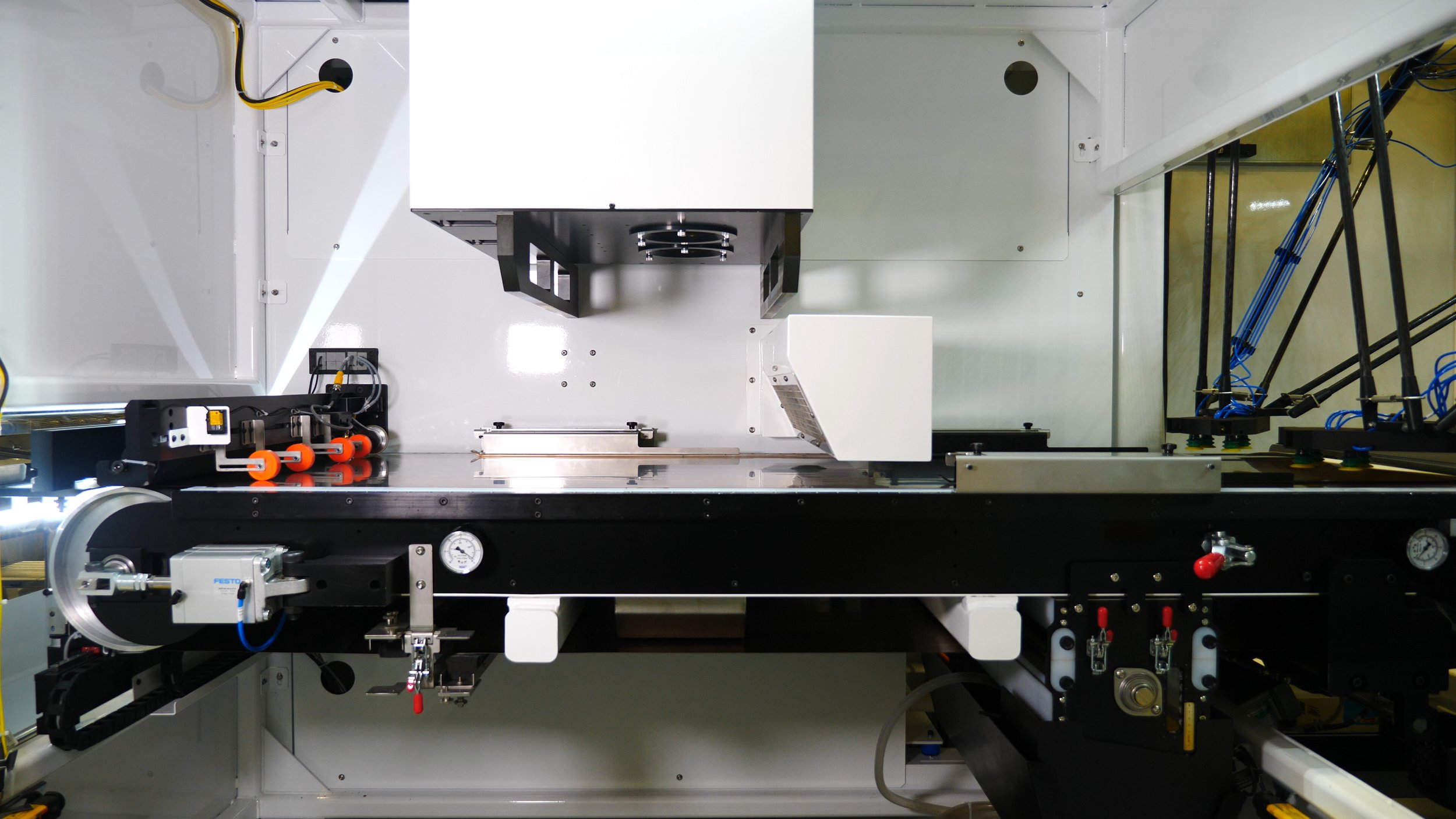
Patented metal belt
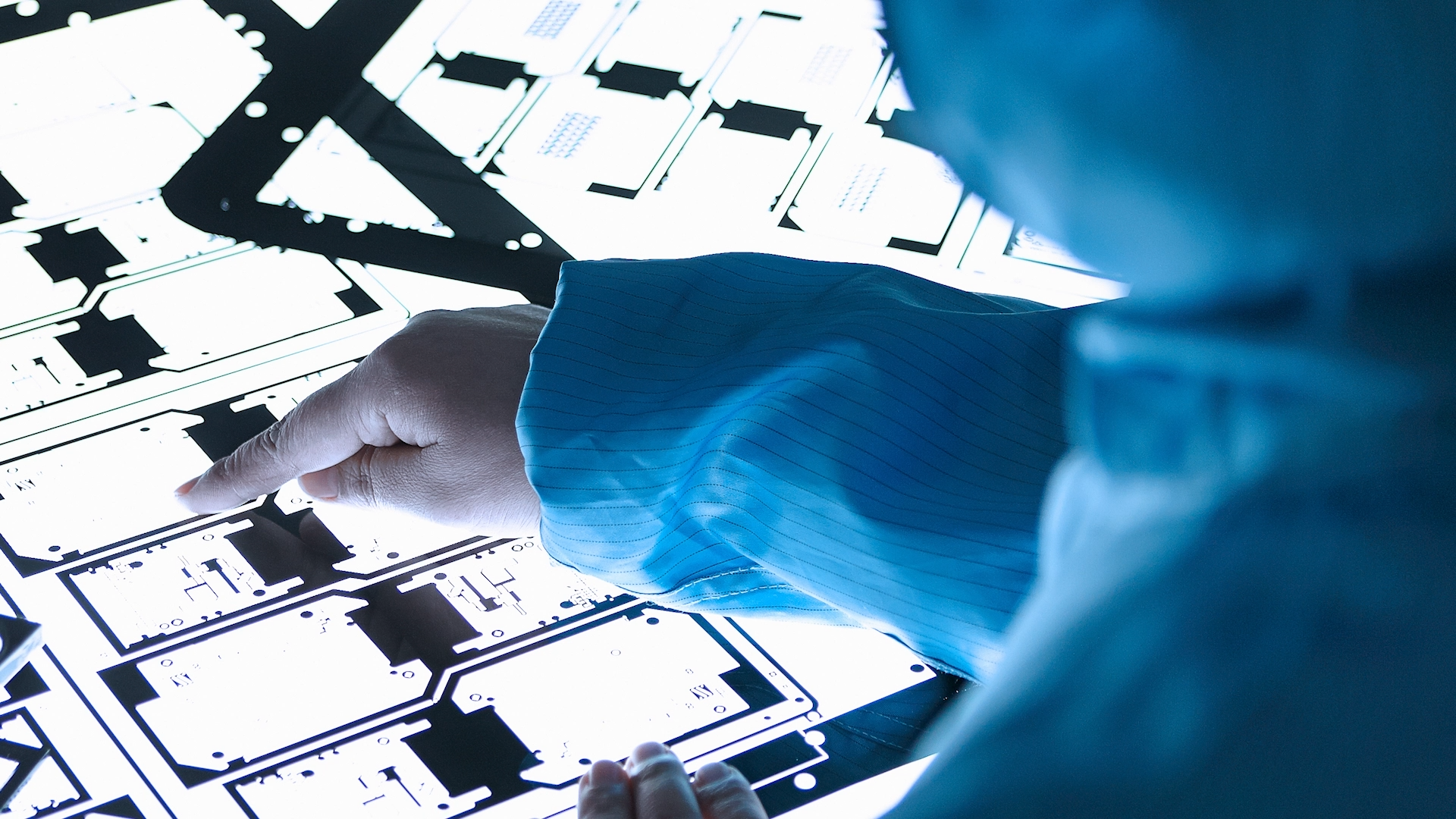
Laser cutting of flexible electronics
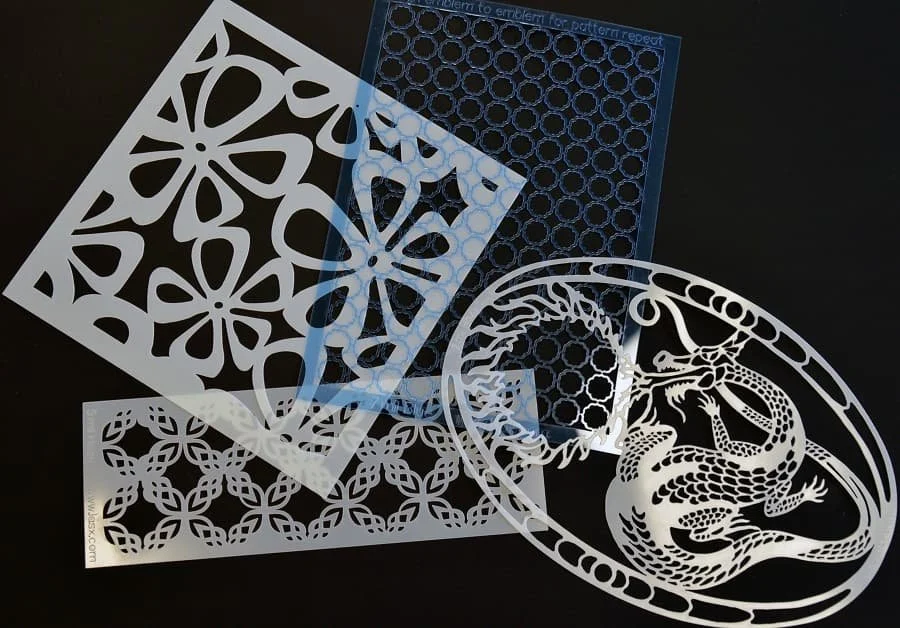
Intricate stencil cutting
Our Laser Processing Capabilities include:
Through-Cutting
•
Drilling/Micro-Perforating
•
Scoring
•
Ablating
•
Kiss-Cutting
•
Etching/Marking
•
Through-Cutting • Drilling/Micro-Perforating • Scoring • Ablating • Kiss-Cutting • Etching/Marking •
The LasX Story
Back in the 1990s, we recognized a big gap in the manufacturing industry — the lack of a flexible, modular option for laser material processing. At the time, existing off-the-shelf solutions fell short in their ability to synchronize the laser, material interaction, and part handling in real time. To solve this issue, LasX was founded in 1998 and soon after, the LaserSharp Processing Module (LPM) – which is the core engine for delivering our innovative processing solutions – was launched.
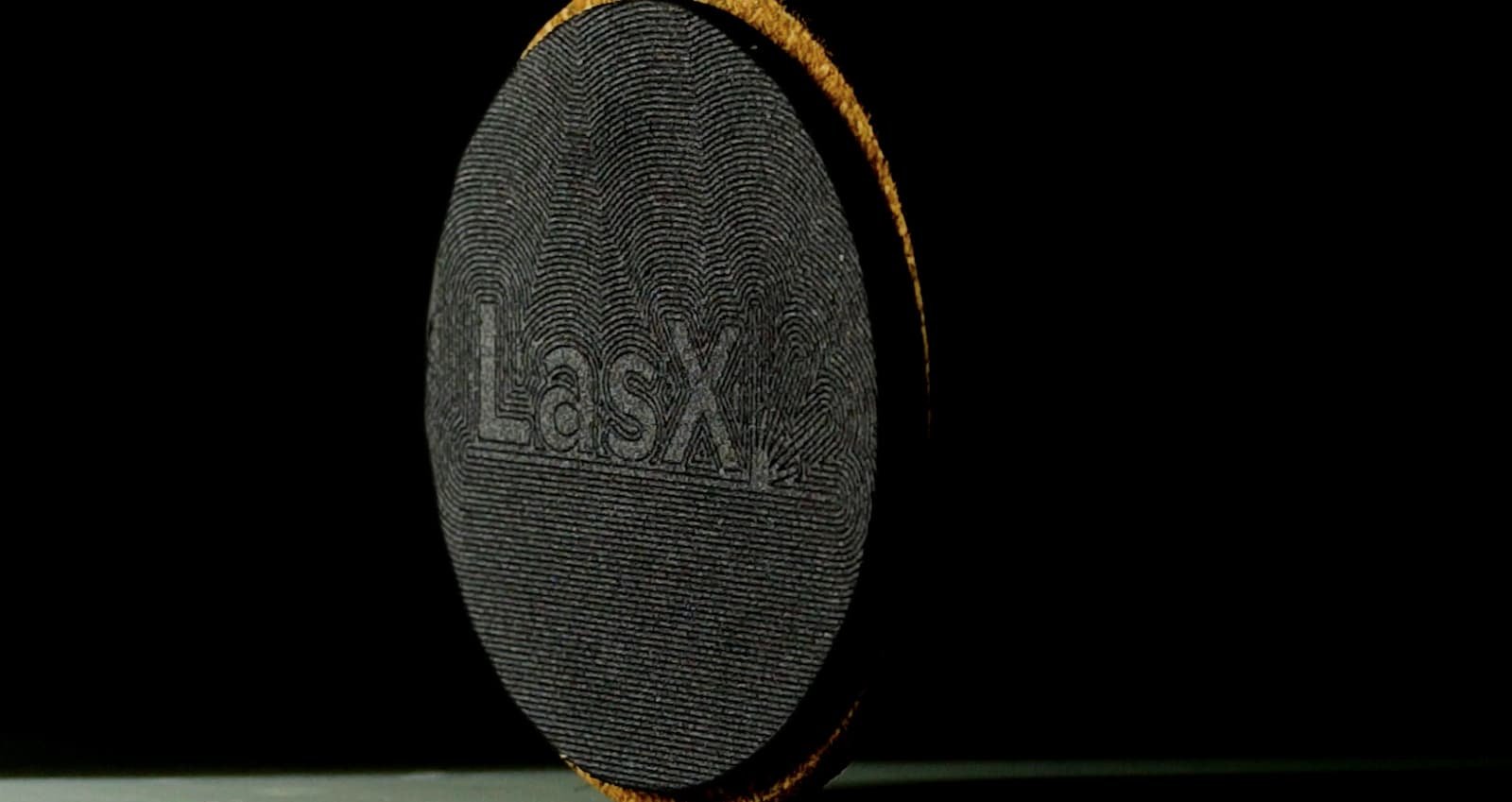
Material Processing Capabilities
Elastomers
Nonwoven Fabrics
Silicones
Urethanes
Ceramics
Rubber
Papers
Plastics
Adhesives
Metal Foils
Textiles
Foams
Teflon
Mylar
Nylon
VHB adhesives
Kapton®
Kevlar®
Felt
Leather
Cork
Graphite
Prepare for the future with LasX.
-
Implementing smart manufacturing techniques and sophisticated automation is essential for manufacturers to remain competitive. LasX recognizes this, which is why we design technology for facilitating fully digitized converting and finishing processes.
-
The LasX technology roadmap is committed to promoting sustainability initiatives. Our forward-thinking vision takes into consideration material waste, production waste, and viability of environmentally-friendly materials.